Food & Beverage Consulting
The Food and Beverage Industry and the Cannsult Value Proposition
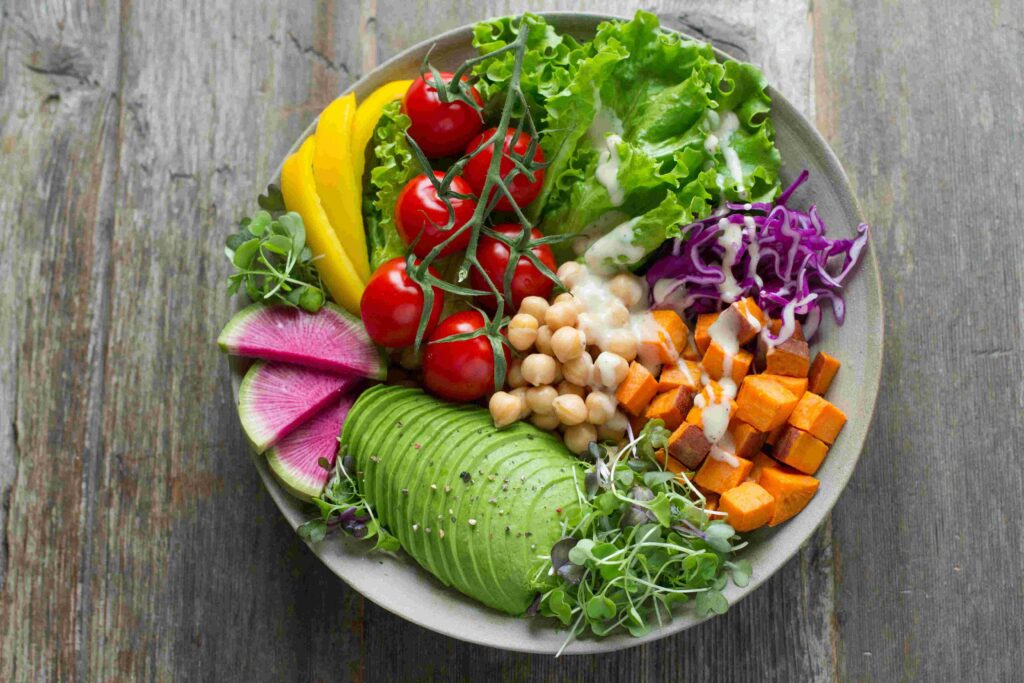
Cannsult Understands the Food and Beverage Industry
Cannsult has worked with some of the most prominent players in the Food and Beverage industry, startups, and entrepreneurial ventures. We have supported organizations in various sub-sectors such as agriculture, food, and flavors processing and distillation. Continuous improvement has a significant impact on this industry. By striving for ongoing enhancements in various areas, such as quality, efficiency, safety, and sustainability, businesses in this industry can gain a competitive edge and meet the evolving needs of consumers.
How we work with you to improve your organization
01
Discovery and Planning
02
Prepare Leaders and Infrastructure
03
Implement Daily Problem-Solving
04
Root Cause Analysis Projects
Discovery and Planning
- Understand the organization. (Type of Manufacturing, Customer/Market, Company History, Org Structure)
- Understand your organizational goals.
- Understand current challenges and risks facing your organization.
- Meet the team and understand resource constraints.
- Prepare a high-level plan including scope, timeline, resources required, and expected ROI.
- Solidify Statement of Work.
Prepare Leaders and Infrastructure
- Understand current infrastructure to support improvements. (if any)
- Identify internal Continuous Improvement Lead(s).
- Meet with each Departmental or Business Unit Leader. (in scope)
- Perform an initial Assessment to identify opportunities and to be used as a baseline.
- For each Department/Business Unit:
- Â Create a high-level process map.
- Identify KPIs. (aligned with Organizational goals)
- Establish Visual Performance Management. (A graphical representation of KPIs)
- Perform a Gap/Opportunity Assessment.
- Prioritize Gaps and Opportunities.
- Provide training to leaders (Sponsors, Champions) who will be supporting the Improvement Teams. (2-day training)
- Provide stakeholder training; a high-level overview of the method, tools, and terminology to ensure organizational alignment. (2-hour training)
Implement Daily Problem-Solving
Select initial areas of focus, Departments, Functions, or Work Areas. Which may include core functions, Engineering, Supply Chain, Production, Quality, etc. And/or support functions, HR, Technology, Finance/Accounting, Legal, etc.
Prioritize and scope based on impact on organizational goals, logical sequence, and resource availability.
Select initial daily problem-solving teams.
Provide training for daily problem-solving teams. (5-day training)
Implement Daily Problem-Solving and Visual Performance Management in each selected area.
Identify issues to be escalated; issues that require a higher skill level to resolve. (E.g. cross-functional issues, high complexity, high risk, high cost, etc.)
Root Cause Analysis Projects
With Departmental Leaders, prioritize escalated issues based on impact, logical sequence, and resource availability.
Select initial Root Cause Analysis (Green Belt) teams.
Provide Green Belt Training (Root Cause Analysis project training) for selected team members; Projects launched during training. (8-day training)Â
Provide project direction and support throughout the project duration. (Estimate 3 to 4 months for each improvement project)
Provide direction and support through project closure.
Validate improvement results and calculate ROI.
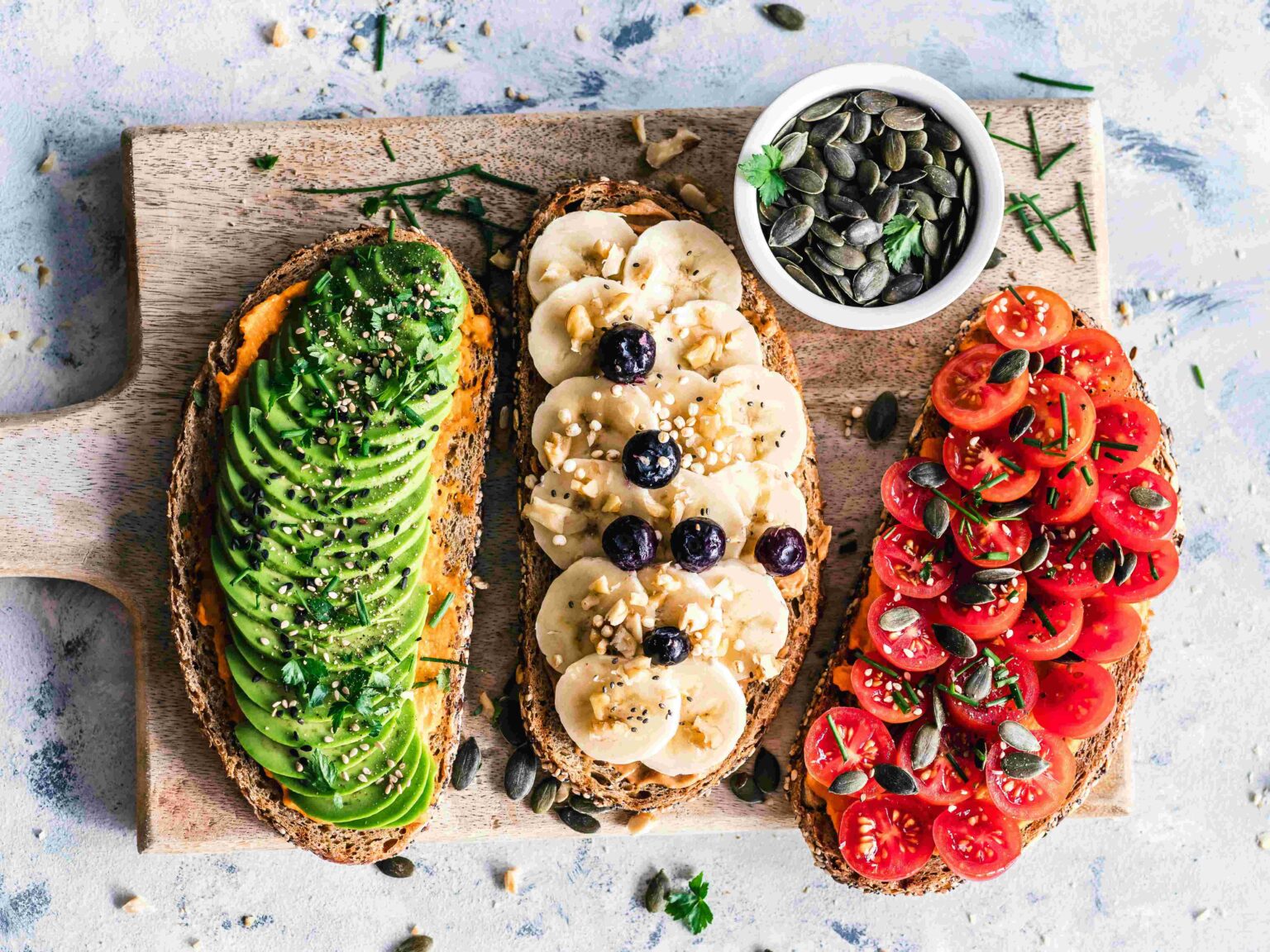
cannsult improvement examples (quick version)
- The Citrus Distillation process improved from 4 steps (65 hours) to 2 steps (24 hours).
- Decreased material costs from $774k to $574k.
- Improved Distillation Process Yield from 3.7% to 63%.
- Improved Liquid Materials Flow and Returns.
- Reduced Shop Floor Discards.
- Reduced Quality Discards.
- Reduced Cycle Time for Raw Materials Compounding.
- Improved Material Flow Efficiency: Admin and Shipping.
- Utility Cost Reduction.
- IT Procurement Support Center Harmonization.
- Improved Accuracy of Inventory Data.
- Improved Local and Regional Consumer Products Cycle Time.
- Increased Efficiency and Quality of Difficult to Make Items.
- Improved Heat Room Layout and Sourcing.
- Increased Material Optimization.
- Increased Pouring Utilization. (Consumption of Full Packs and Pack Reduction)
- Reduced Replenishment Defects.
- Improved Large Batch Throughput.
- Reduced Consumable Costs (by $22k) and Increased Capacity by 35%.
- Increased Automated Compounding.
- Reduction of Large Batch Shortages. ($110k savings)
- Reduced Equipment Idle Time.
- Reduced Internal Non-Conformances.
- Reduced Robot Processing Defects.
- Supply Chain Improvement: Increase Raw Materials available 48 Hours before Due Date.
- Reduced Cycle Time and Increased Accuracy of Order Entry.
Similarities between Food and Beverage and other industries
When creating a culture of Continuous Improvement, in some ways, the Food and Beverage industry is no different from any other industry in that the same high-level steps apply.
Get our Lean6sigma Certification Online
via Hybrid Platforms
Our Comprehensive Training Programs are now available on iOS, Android, and a Web platforms.
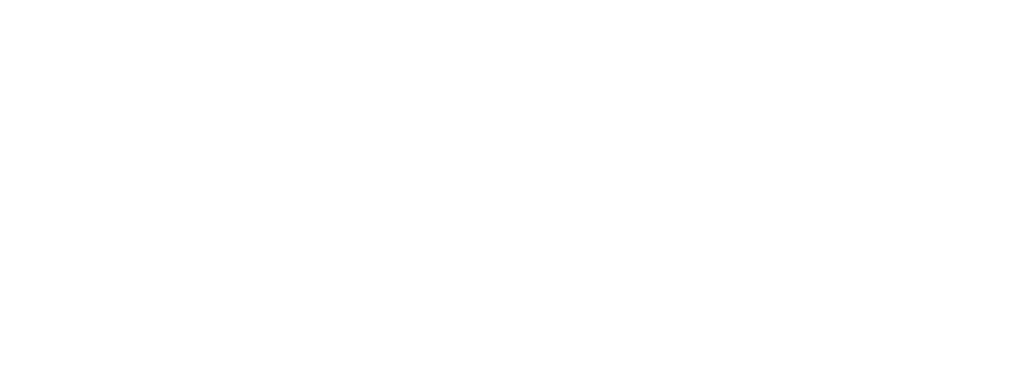
Testimonials
How our Customers React?​
Have a look at how Cannsult transform their Partners businesses and help them achieve their business Goals.
Lorem Ipsum is simply dummy text of the printing and typesetting industry. Lorem Ipsum has been the industry’s standard dummy text ever since the 1500s, when an unknown printer took a galley of type and scrambled it to make a type specimen book. It has survived not only five centuries, but also the leap into electronic typesetting, remaining essentially unchanged. It was popularised in the 1960s with the release of Letraset sheets containing Lorem Ipsum passages.
Carolyn Willms​
Global Accountability Officer
Lorem Ipsum is simply dummy text of the printing and typesetting industry. Lorem Ipsum has been the industry’s standard dummy text ever since the 1500s, when an unknown printer took a galley of type and scrambled it to make a type specimen book. It has survived not only five centuries, but also the leap into electronic typesetting, remaining essentially unchanged. It was popularised in the 1960s with the release of Letraset sheets containing Lorem Ipsum passages.
Carolyn Willms​
Global Accountability Officer
Lorem Ipsum is simply dummy text of the printing and typesetting industry. Lorem Ipsum has been the industry’s standard dummy text ever since the 1500s, when an unknown printer took a galley of type and scrambled it to make a type specimen book. It has survived not only five centuries, but also the leap into electronic typesetting, remaining essentially unchanged. It was popularised in the 1960s with the release of Letraset sheets containing Lorem Ipsum passages.
Carolyn Willms​
Global Accountability Officer
Lorem Ipsum is simply dummy text of the printing and typesetting industry. Lorem Ipsum has been the industry’s standard dummy text ever since the 1500s, when an unknown printer took a galley of type and scrambled it to make a type specimen book. It has survived not only five centuries, but also the leap into electronic typesetting, remaining essentially unchanged. It was popularised in the 1960s with the release of Letraset sheets containing Lorem Ipsum passages.
Carolyn Willms​
Global Accountability Officer
Lorem Ipsum is simply dummy text of the printing and typesetting industry. Lorem Ipsum has been the industry’s standard dummy text ever since the 1500s, when an unknown printer took a galley of type and scrambled it to make a type specimen book. It has survived not only five centuries, but also the leap into electronic typesetting, remaining essentially unchanged. It was popularised in the 1960s with the release of Letraset sheets containing Lorem Ipsum passages.
Carolyn Willms​
Global Accountability Officer
Lorem Ipsum is simply dummy text of the printing and typesetting industry. Lorem Ipsum has been the industry’s standard dummy text ever since the 1500s, when an unknown printer took a galley of type and scrambled it to make a type specimen book. It has survived not only five centuries, but also the leap into electronic typesetting, remaining essentially unchanged. It was popularised in the 1960s with the release of Letraset sheets containing Lorem Ipsum passages.
Carolyn Willms​
Global Accountability Officer
Let's Connect
Thank you for your interest in Cannsult Inc. If you have any questions or want to know more about us, please send us a message.
- (561) 890-2235
- info@cannsult.org
- Melbourne, Florida, 32940, USA