FMEA Meaning, Usage, Simple Example, and Free Template!
A key element of process improvement and process design is to create a process that prevents problems from occurring, or that can at least detect issues early in the process. There are many different tools to mitigate the risks in a process, and our topic today will cover the most robust, which is the FMEA process. This tool can be used in very simple ways, or it can be extremely intricate and robust, depending on the complexity and level of risks in your process. It can be sketched on a piece of paper or done in a detailed spreadsheet or software. The FMEA process provides the discipline to identify all those things that can fail in your process and then provides the structure to prioritize and plan for mitigation.
What is FMEA?

FMEA stands for Failure Modes and Effects Analysis. It is a technique adapted from the aerospace industry to help more effectively anticipate and avoid problems. While often delivered in a way that can seem overly complex, it is in fact a fairly simple tool. FMEA has been applied to almost every industry and is simply a method to assess and plan for problems that could impact safety, reliability, customer satisfaction, profits, etc. It is also a tool for process owners to allocate measurement and prevention resources (normally put into place in the Control phase of DMAIC). The main attraction of FMEA comes from the fact that it focuses on prevention rather than fire fighting, and ultimately promotes better solution implementation and more proactive ongoing management.
The FMEA process typically involves a workshop with the project team. The duration and format of the workshop will totally depend on the size, complexity, and risk in the process that is being improved or designed. The FMEA process takes place after detailed process mapping when analyzing the current state and when designing the future state.
Reviewing each step of the process, the team will brainstorm ways in which the process can fail. For example, if the process step is to “Open the Application”, a failure might be “application will not open”. The team will identify all the possible failure modes or reasons why the application will not open. For example, “User Login Failed” or “Network Unavailable”. When the list of possible failures is captured, the team will move to the next step of evaluating the potential failures or risks.
The Failure Mode and Effects Analysis process provides a structure for the team to evaluate each risk based on three criteria;
-
Severity: Describe the impact or consequences if this failure occurs. This allows the team to specify the impact of this problem by evaluating the safety, quality, time, cost, or efficiency implications.
-
Occurrence: The occurrence specifies the likelihood that failure will occur over time. What is the expected frequency or probability that this particular failure will happen? For example, the team will likely have a different rating for Occurrence for “User Login Failed” and “Network Unavailable”.
-
Detection: The Detection is the probability that the failure could be detected promptly if it occurs (or before it occurs). Some failures can be easily detected ahead of time (which makes them less risky) and others can be very difficult to detect. This evaluation allows the team to recognize that the harder a failure is to detect, the greater the risk.
The FMEA steps are as follows
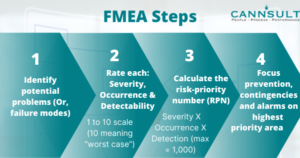
-
Identify potential problems or “failure modes”; Focus on critical or complex steps and key requirements, List the potential “failures”. In this step, the team will use their selected choice of brainstorming methods to gather a comprehensive list of potential reasons for the process step failing. How many reasons can you think of why your car won’t start? Maybe you have the wrong key, the gas tank is empty, the battery is dead, etc. These are all different failure modes for “Car Won’t Start”.
-
Rate each: Severity, Occurrence & Detectability; 1 to 10 scale (10 meaning “worst case”), Helps to “operationally define” the scale. Each of the failure modes will be evaluated against the Severity (to assess how bad the impact is), the Occurrence (to assess the likelihood), and the Detectability (the harder to detect, the greater the risk). Our free template provides “Anchor Tables” to provide a description of the 1 to 10 ratings for each of these criteria. This rating will be our mechanism to recognize the most critical failures, so the team can prioritize their risk mitigation.
-
Calculate the risk-priority number (RPN); Multiply Severity x Occurrence x Detection (max = 1,000). Each of the failure modes will have been rated (on a scale of 1 to 10) for Severity, Occurrence, and Detection. For example, for our “gas tank is empty” failure mode, the team may have rated the Severity an 8 (because we’d be late for work), the Occurrence a 2 (as it happens infrequently), and the Detection a 1 (since there is an indicator on the dashboard). If we multiply 8 x 2 x 1, the overall Risk Priority Number would be 16.
-
Focus prevention; contingencies and/or alarms on highest priority areas. With all the RPNs calculated for each Failure Mode, the team can sort by the highest RPN and begin the process of improving the process to prevent the failure modes from occurring wherever possible, or to create a plan for the early detection where a complete failure mode elimination is not possible.
Read more: The Top 5 Continuous Improvement Principles.
FMEA Simple Example
So let’s say you have a big meeting with a client coming up to present a brand new mobile app, and you want to anticipate and avoid all the problems that could occur to mess the big moment up. What a perfect time for an FMEA!
While often delivered in a way that can seem overly complex, FMEA is in fact a fairly simple tool.
Looking back at the FMEA steps, you must first identify the failure modes (potential problems) from the beginning of the process (or in this case, the big day). You come to the conclusion that being late for the meeting would be the first potential problem. After rating, calculating, and finally coming up with your RPN (risk priority number). We can simply visualize the process like this;
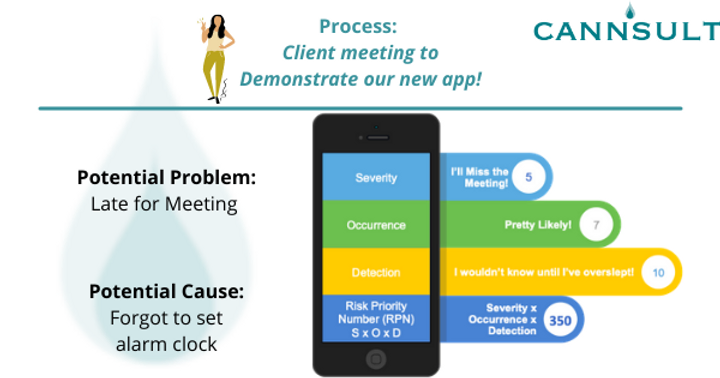
With that high “detection” rating and high “occurrence”, that RPN is a little too high for comfort, but let’s keep going with the process. Another potential problem could be that during the presentation, the mobile app isn’t working! Here is another simple way to visualize our FMEA;
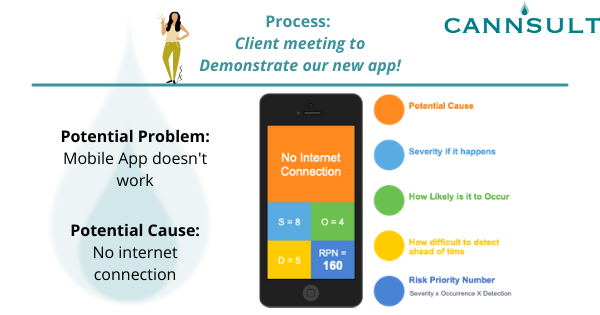
By going through the FMEA process, we can see that our highest priority problem here is being late for the meeting. Now, how to go about avoiding these problems? Let’s just say that’s a whole different skill set…
Of course, problems that modern-day organizations run into are much more complex than presenting a mobile app, but the same concept can be applied to the most complex of problems. Below is a real and practical example of a completed FMEA.
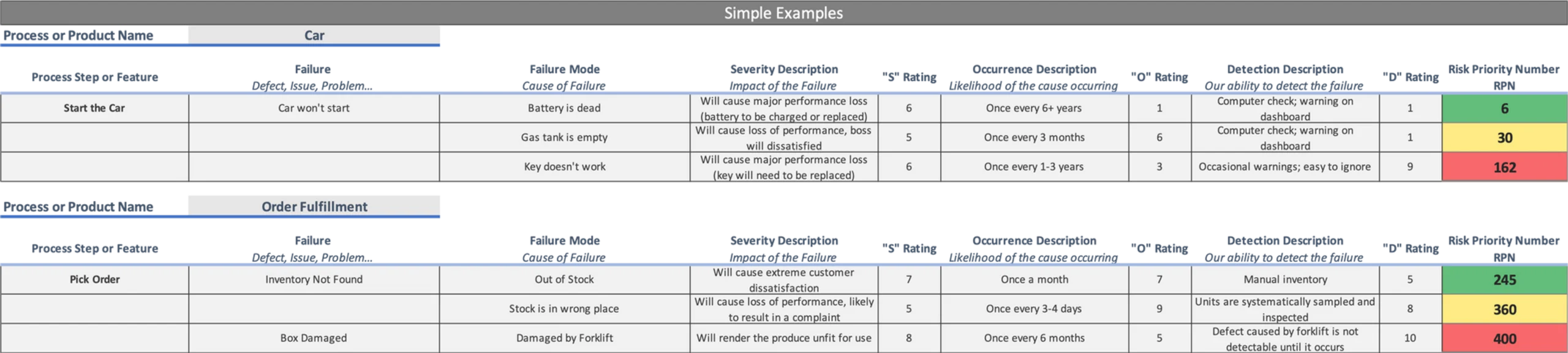
Enroll in our online business development courses and become a certified incredible leader!
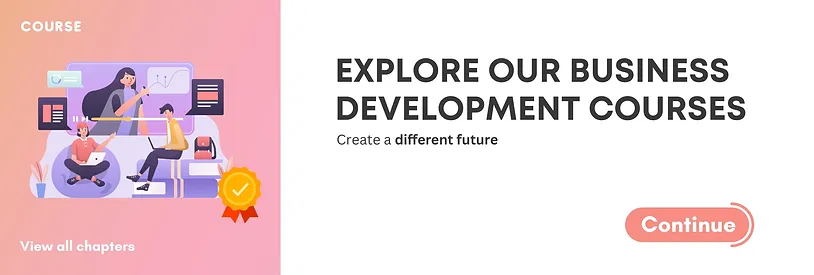