Across the globe, we share a fundamental opportunity; educational systems need dramatic improvement…no more tinkering, and no more massive efforts that fail. Schools and school districts are complex, dynamic systems affected by tons of factors. Efforts to improve (small and huge) are everywhere, but a very limited number proves to be effective. From controversial federal policies to individual teachers adopting new innovative techniques, it can be a real challenge to measure the success of educational interventions and even more difficult to understand why so many fail.
The complexity of education is commonly underestimated. Attempts to improve are often designed outside of the intended school or are copied from other schools, only to fail in the context of the implementation. There are many factors that can impact the outcome of an attempted improvement, including the characteristics of the individual students, the participation of the educators, the socioeconomic status of the community, the administration’s beliefs and behaviors, the standardized testing regime, the level of parental involvement, and so on. In spite of the complexity of these systems, most efforts to improve ignore the importance of quantitative methods to deliver meaningful and sustainable solutions.
In spite of the complexity of these systems, most efforts to improve ignore the importance of quantitative methods to deliver meaningful and sustainable solutions.
Our objective, as with all industries and types of organizations, is to utilize a framework that will help educational decision-makers and teams clearly understand problems and opportunities and to have the competence to apply proven methods to truly make things better. No single solution is applicable across the broad spectrum of school settings. However, Lean Six Sigma provides a unified method that allows the educational teams to create sustainable solutions for their own particular contexts. Two decades of experience in applying Lean Six Sigma demonstrate how this improvement method (that originated in manufacturing) can have dramatic results in education – something that hits home to absolutely everyone.
Most organizations, including schools and school systems are constantly working on solving problems and better ways of working. The question is not whether you’re working on it – we know that you are! The question is how effective are your efforts. Are the issues getting rapidly resolved? Are students developing? Are they learning and becoming more competent? Are they happier? Are the parents and caregivers engaged and aligned? Is the staff engaged and feeling like they have a fulfilling work life? If not, then it’s time for a proven method to make those ideas a reality.
Implementing Lean Six Sigma means that practices are in place to provide direction and support to a small but critical number of certified problem-solving specialists sprinkled throughout the organization. This may sound daunting and costly. But, it shouldn’t be! If the implementation is a disruptive and massive undertaking, it’s not being done right! The implementation of Lean Six Sigma should be the epitome of a highly efficient process with exceptional results.
Here, we discuss the 4 high-level steps to a Lean Six Sigma implementation in a health care organization:
A very powerful feature of a Lean Six Sigma implementation is the creation of an infrastructure to assure that performance improvement activities have the necessary resources. Everyone in your organization doesn’t need to be a certified Lean Six Sigma expert. But in order to succeed and to get the greatest return, there has to be a support system. Some experts estimate that failure to provide this infrastructure is the #1 reason why improvement efforts fail. The Lean Six Sigma infrastructure makes improvement and change the full-time job of a small but critical percentage of the organization’s personnel. And then supplements the full-timers with just enough expertise and support system to make it all work.
Some experts estimate that failure to provide this infrastructure is the #1 reason why improvement efforts fail.
Step 1: Discovery & Planning
Understand Organizational Goals and Current Scenario and Align the organization with Lean Six Sigma White Belt Certification
The basis of any decisions and actions taken by anyone in the organization should be driven by the foundational goals of the organization. What is the organization aiming to achieve in the next 1, 3, and 5 years? Greater quality of care? Access to care? Growth? Reduced Costs? Expansion into new technologies? New specialties? If the aims of the organization have not been clarified, then that’s the starting point. We first solidify the organization goals and then we understand the current scenario – in other words, we understand the size of the gap between the current reality and the goals. And that gap between current reality and the organizational goals is the thing that we’re going to close!
…solidify the organization goals and then we understand the current scenario – in other words, we understand the size of the gap between the current reality and the goals. And that gap between current reality and the organizational goals is the thing that we’re going to close!
To get it going, everyone in the organization – first leaders, then everyone else – gets involved, gets aligned and speaks the same language. This is done through a quick and easy Lean Six Sigma White Belt Certification.
Step 2: Prepare Leaders & Infrastructure
Lean Six Sigma Blue Belt (Sponsor) Training & Certification
Without the demonstrated and skilled support of leadership, the opportunities for success are poor, which means that any attempts to solve problems will be minuscule, costly or unsustainable. To define leadership and efficient and effective decision-making, we start by establishing a Steering Committee. This is the group of leaders who will solidify the organizational strategy to achieve major goals and to provide direction and support to ensure successful improvement projects that support those goals.
To ensure the greatest efficiency and outcomes of this process, Functional Leaders (typically 2% of the organization) learn consistent and proven methods and tools to successfully sponsor improvement projects. This is accomplished through Lean Six Sigma Blue Belt (Sponsor) Certification.
Through the Lean Six Sigma Blue Belt (Sponsor) Certification process, the cross-functional leadership will create high-level functional maps, identify KPIs and implement basic Visual Performance Management (VPM) for each department.
Without the demonstrated and skilled support of leadership, the opportunities for success are poor, which means that any attempts to solve problems will be minuscule, costly or unsustainable
Step 3: Implement Daily Problem-Solving
Lean Six Sigma Yellow Belt Certification
With Visual Performance Management (VPM) in place for each of the major departments, organizational leadership will have the tools and process in place to prioritize and plan for functional daily problem-solving.
Daily Problem-Solving is a very efficient method used by frontline employees and supervisors to prevent issues, have a mechanism to detect issues early and, when issues are detected, to be ready with a quick and effective response. Applying these skills can prevent and solve up to 80% of issues that – if unaddressed – will grow into complex and systemic issues.
Daily Problem-Solving is a very efficient method used by frontline employees and supervisors to prevent issues, have a mechanism to detect issues early and, when issues are detected, to be ready with a quick and effective response.
To learn the tools and methods to achieve stunning results, frontline employees and supervisors (typically 25% of the organization) complete Lean Six Sigma Yellow Belt Certification. As a result of the training and certification, quick and highly productive daily problem-solving meetings will be ready to go.
Some examples of problems that have been solved by the Cannsult Yellow Belts are:
-
Reduce time to transfer patients
-
Eliminate meds not moving with patients
-
Increase billing accuracy for Peri Op Billing
-
Increase compliance with 16 high-touch audit
-
Increase % complete Pre-surgical Chart Review
-
Increase accurate/complete Surgery Chart data
Step 4: Launch & Support Root Cause Analysis Projects
Lean Six Sigma Green Belt Certification
With daily problem-solving in place, frontline employees and supervisors will be skilled in quickly and accurately identifying issues that require additional skills to resolve. These are typically more complex, cross-functional, or systemic issues that require root cause analysis. To successfully resolve these issues, team leaders or selected participants (typically 5% of the organization) complete Lean Six Sigma Green Belt certification.
Lean Six Sigma Green Belts are project leaders capable of forming and facilitating Lean Six Sigma teams and managing larger root cause analysis projects from concept to completion. A Green Belt is typically not a full-time project position. This means that they have their full-time job (a Nurse, Respiratory Therapist, Call Center Rep…whatever) but they also lead or participate in improvement projects in addition to their main role. Green Belts typically complete 2 projects a year with an average value of about $75,000 for each project. As a part of the training and certification, Green Belt projects are launched and supported by Leadership.
Green Belts typically complete 2 projects a year with an average value of about $75,000 for each project.
Some examples of complex problems that have been solved by Cannsult Green Belts are:
-
Eliminate unnecessary transfers post PCI to ICU
-
Improve Cath Lab patient flow
-
Eliminate multiple discharge orders
-
Improve Room Readiness – Meds, biohazards Removed, Clean Room
-
Improve patient throughput: Reduce admission wait times
-
Identify patient risk factors and increase participation in preventive programs
With so much health care improvement just waiting there to be done, with so much patient, community and employee contentment waiting to be achieved, it’s a terrible thing to wait until we feel ready. In our experience, no one is really ever ready to do anything. We have to approach improvement as if there is no such thing as “ready”. There’s only such thing as now!
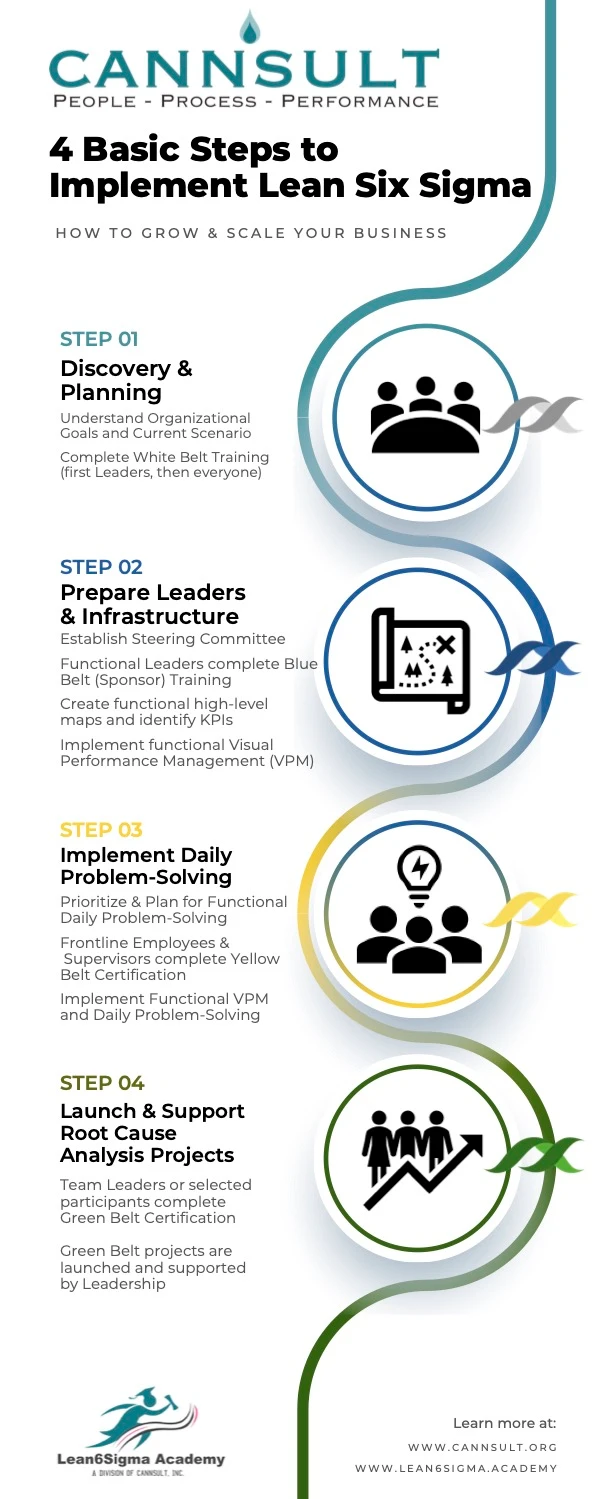