It’s been another interesting week causing us to pause and regroup on the topic for this blog. In the past few days, we’ve defended Lean Six Sigma from cynics who say that it’s all smoke and mirrors and have worked with multiple prospects discussing different shortcut approaches to solve their crushing pressures and challenges. And while I’d love to say that creating a culture of continuous improvement is really complicated, it’s just not. Like anything else that’s worth doing, it will work, but only if you do it right. Do it or don’t do it, but you have to commit.
Would you have surgery by someone who dabbled in medicine? Would you hire a homebuilder who simply watched a few seasons of Flip or Flop? Come on, man!
Lean Six Sigma is a proven organizational improvement method that has demonstrated billions of dollars in tangible improvements and even more in intangible improvements. Yes, I know. Many of us have seen it fail. And that’s because the decision-makers didn’t commit. They did some of it. They tried a shortcut, and it didn’t work.
The benefits of Lean Six Sigma are real. And while the dollars are always important, that’s just one of the many benefits. Implementing Lean Six Sigma the right way means that you will see priceless results materialize. Like what? Like increased employee competence and engagement, skillful collaboration and teamwork, increased productivity, high-quality, decreased costs, increased revenue, speedier delivery, increased safety, tighter security, and minimized risks. And along with this comes the energy and enthusiasm that you get from competent “A” Players, who are confident and excited about their work.
How to Implement Lean Six Sigma
A Lean Six Sigma Implementation means that an organization commits to delivering excellent products and services and becoming a workplace full of self-reliant achievers. And there’s a clear roadmap and method to do just this. The belt levels of Lean Six Sigma describe that a certain proportion of the organization needs to have specific skills; daily problem-solving, root cause analysis for complex issues, and leadership skills to support them. Not everyone needs to be an expert, but everyone has their own role and contribution.
Here’s a quick rundown of the different belt levels and the recommended proportion needed in an organization.
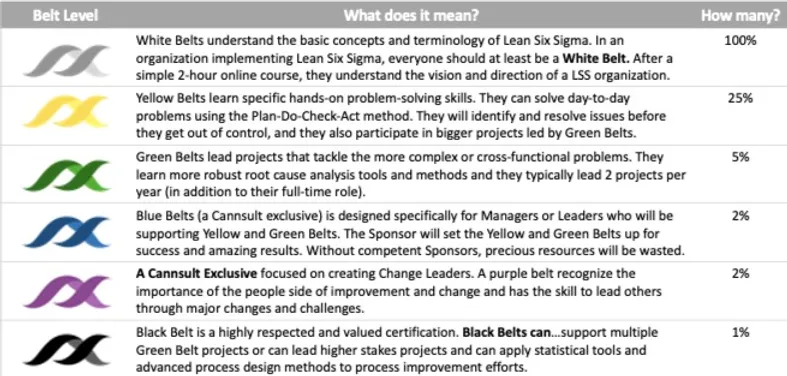
So, just to illustrate with a little graphic, in an organization of 100 people, the proportion of belt levels would look something like this:
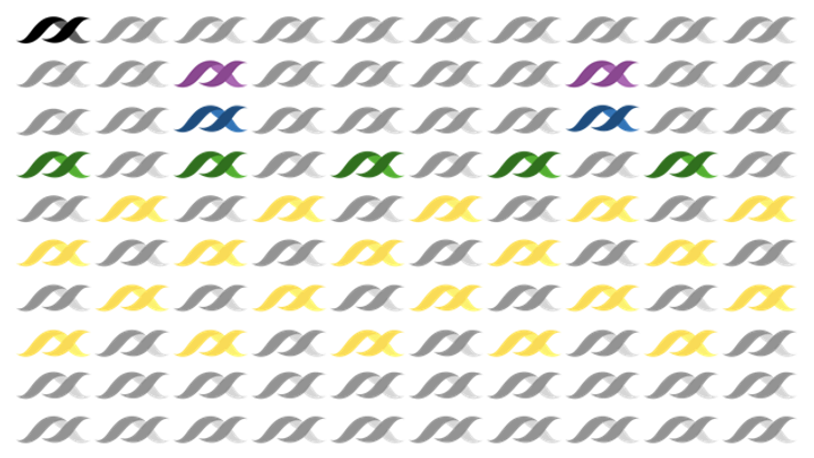
With this foundation in place, an organization will have the ability to successfully identify problems and opportunities and then quickly implement sustainable and meaningful improvements. The organization will become an enjoyable workplace, people will know how to work together and collaborate to solve problems. Chaos, firefighting, and building frustrations and blame will dissipate as teams see their efforts materialize into truly meaningful results.
Keys to Proper Implementation
I can tell you this isn’t all done by dabbling in it or doing it a little. It’s not done by having a couple of people read a few books or pass an exam. It’s a system and it needs all its parts functioning.
-
The right number of the right people need to be properly trained.
-
The people who are trained need the time and the space to practice what they’ve learned.
-
Leadership must actively support the roles and methods.
How long does Lean Six Sigma Training take?
The training is the first chunk of time that is required. And then training is followed by a period of practice and initial setup of the new ways of working. With the right training and support, after a short online course, Yellow Belts can be up and running in a matter of weeks. This means that they will be actively working as a team to solve daily problems as they arise. For Green Belts, the training is more intensive (40 to 60 hours). And, depending on the scope, they can complete their first project in 3 to 4 months. Sponsors (Blue Belts) will learn the tools and structure to actively support Yellow and Green Belts in a power-packed 2 days.
How much does Lean Six Sigma Training cost?
In the above illustration, we show an organization of 100 people with the recommended distribution of the different belt levels. To accomplish this exact model, the training investment would be about $12,000. The time to practice and set up new ways of working depends on the specific organization and level of leadership support.
What are the benefits?
As my partner likes to say, “How long is a piece of string?”. Going by averages, a single Green Belt typically completes 2 projects per year at an average benefit of $75k per project. A typical Black Belt will complete 5 projects per year at an average benefit of $150k per project. Not all projects result in hard financial benefits. Projects will also focus on other Key Performance Metrics such as Productivity, Quality, Timeliness, Safety, Security, and Legal Compliance to name a few. So without getting too technical with the financial calculation of ROI, we can confidently say that for an investment of $12k, plus the investment of time for practice, the projects that come out of this investment in the first 12 months can be expected to be north of $1m. And that doesn’t even account for all of the daily problem-solving that is nipping issues in the bud and most importantly, the intangible benefits of creating a culture of highly competent and highly engaged employees and teams.
To see these benefits materialize, we can’t take a shortcut or kinda sorta do it. The return will be a big waste of resources and will result in employee frustration and fatigue with failed attempts to improve. So do it! Or don’t. Just don’t get yourself caught in the middle!
Real-World Examples of Lean Six Sigma Results
Healthcare
Lean Six Sigma has been used to drive success by minimizing delays, repetition, and mistakes that ultimately affect patient care. In private, non-profit, and government healthcare facilities, Lean Six Sigma has been used to recognize, prioritize and address the many opportunities for improvement. Reduced wait times in the Emergency Department, drastically reduced infection rates, increased time with patients and doctors, ready supplies, reduced time for discharge, employee engagement, and faster and more effective hiring are just some examples of Lean Six Sigma success in healthcare.
Banking
In this highly transactional industry, customers have access to their banking systems in the palm of their hand. Lean Six Sigma has been implemented across the banking industry to improve – not only the basic requirements of fast and accurate – but also to improve the overall customer experience. Projects in banking have included the development of banking apps, going paperless, providing easy access to important information about options, and fraud prevention among many others.
Fragrances
Developing a fragrance starts with an idea or a concept and ends up with a product on a shelf, which becomes part of our life, whether it’s the clean smell of our shampoo, our laundry detergent, or our finest going-out perfume. The biggest players in the fragrance industry have recognized the importance of Lean Six Sigma. In addition to the common efficiencies gained in a manufacturing environment, the fragrance industry has realized improvements such as shrinking the timeline from concept to selected fragrance, improving the quality through rapid lab tests and collaboration with perfumers, increasing the number of sample fragrances that can be used as stock fragrances.
Education
School systems across the US are only recently becoming aware of the advantages of Lean Six Sigma and we have been fortunate enough to have provided guidance and support to multiple school districts. In addition to improving the core focus of improving the student experience and grades, they have had great successes in supporting functions such as reducing the cycle time for hiring, decrease in the % of Special Education students missing core instruction, increase % of teachers integrating ACT results into prep instruction, improve Customer Service ratings across all functions, improving the school bus schedule, improve the consistency of grading criteria, developed a new Mentor Program for new teachers, and improvement in the quality of cafeteria food.
Lean Six Sigma is a proven method of problem-solving. Explore how it can be deployed to deliver measurable and meaningful improvements in both customer-facing and internal processes. In this complex and constantly changing environment with so many interconnected dynamics, a skillful implementation of Lean Six Sigma will foster a sustainable culture of continuous improvement. The result will be the development of a highly capable and engaged team with the skills, energy, and enthusiasm to recognize and address issues and opportunities on a regular basis – an integral part of the organizational culture.