In an era where environmental consciousness and resource efficiency are paramount, sustainable manufacturing has become more than just a buzzword; it’s a necessity for businesses looking to thrive in a world with increasingly discerning consumers and stringent regulations.
In this comprehensive guide, we’ll delve into what sustainable manufacturing entails, how to achieve it, the technologies and tools available, essential elements, challenges, best practices, and real-world examples that illuminate the path toward a greener, more profitable future.
What is Sustainable Manufacturing?
Sustainable manufacturing refers to the process of producing goods while minimizing the environmental impact, conserving resources, and prioritizing social responsibility. It’s not only about producing eco-friendly products but also adopting sustainable practices across the entire manufacturing lifecycle.
This approach aligns with the principles of circular economy, where products are designed, produced, used, and recycled in a way that minimizes waste and maximizes resource utilization.
How to Achieve Sustainable Production?
1. Set Clear Sustainability Goals
Begin by defining your sustainability objectives. Whether it’s reducing carbon emissions, conserving water, or minimizing waste, having well-defined goals provides a roadmap for your sustainable manufacturing journey.
2. Adopt Smart Manufacturing and Industry 4.0:
Leverage cutting-edge technologies such as smart manufacturing and Industry 4.0 to optimize processes, reduce energy consumption, and enhance resource efficiency. These innovations enable real-time monitoring, predictive maintenance, and data-driven decision-making.
3. Invest in Sustainable Materials:
Choose materials that are eco-friendly, renewable, or recyclable. Sustainable materials can reduce the environmental impact of your products and enhance your brand’s reputation.
4. Energy Efficiency:
Implement energy-efficient practices and technologies to reduce energy consumption. This includes using energy-efficient machinery, optimizing heating and cooling systems, and incorporating renewable energy sources like solar panels.
5. Minimize Waste:
Adopt lean manufacturing principles to minimize waste generation. Implement recycling and waste reduction programs within your facility, and encourage suppliers to follow suit.
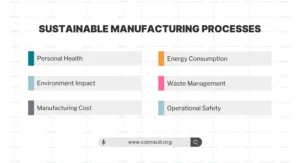
Sustainable Production Technologies and Tools
1. Green Manufacturing Processes:
Utilize environmentally friendly production methods such as water-based coatings, solvent-free adhesives, and low-impact dyes. These alternatives can significantly reduce the use of hazardous chemicals.
2. Advanced Analytics and IoT:
Leverage data analytics and the Internet of Things (IoT) to monitor resource consumption, identify inefficiencies, and optimize production processes in real-time.
3. Life Cycle Assessment (LCA):
Perform comprehensive life cycle assessments to evaluate the environmental impact of your products from raw material extraction to disposal. This data helps in making informed decisions for sustainable improvements.
Collaborate with suppliers that share your commitment to sustainability. Implement responsible sourcing practices and consider transportation efficiency to reduce the carbon footprint of your supply chain.
Elements of Sustainable Manufacturing
1. Resource Efficiency:
Efficiently utilize resources such as water, energy, and raw materials throughout the production process to minimize waste and reduce costs.
2. Reduced Emissions:
Implement measures to reduce greenhouse gas emissions and air pollutants. This not only benefits the environment but can also lead to regulatory compliance and cost savings.
3. Waste Reduction:
Strive to eliminate or reduce waste at every stage of production. Recycling, reusing, or repurposing materials can further enhance sustainability.
4. Environmental Compliance:
Adhere to environmental regulations and standards to avoid fines and penalties while fostering a positive public image.
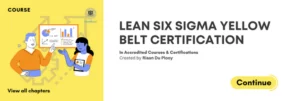
Challenges in Achieving Sustainable Manufacturing
As with any transformative journey, sustainable manufacturing comes with its set of challenges:
1. Cost Considerations:
Initial investments in sustainable technologies and practices may be high, but the long-term savings and benefits often outweigh these costs.
2. Change Management:
Transitioning to sustainable manufacturing requires changes in mindset, processes, and sometimes even company culture. Employee training and engagement are essential.
3. Supply Chain Complexity:
Sustainability efforts must extend to suppliers, which can be challenging to manage, especially if they operate in regions with lax environmental regulations.
4. Measuring and Reporting:
Accurate measurement and reporting of sustainability metrics can be complex but are essential for tracking progress and demonstrating transparency.
Best Practices
To overcome these challenges and build a sustainable manufacturing ecosystem, consider the following best practices:
1. Collaboration:
Collaborate with industry peers, associations, and governmental organizations to share knowledge and resources related to sustainable manufacturing.
2. Continuous Improvement:
Sustainability is an ongoing journey. Continuously evaluate and update your sustainability initiatives to align with evolving standards and technologies.
3. Transparency:
Communicate your sustainability efforts to customers and stakeholders. Transparency builds trust and can enhance your brand’s reputation.

Examples of Sustainable Manufacturing
To illustrate the real-world impact of sustainable manufacturing, let’s explore a few success stories:
The electric vehicle pioneer not only produces sustainable transportation but also focuses on sustainable manufacturing practices. Their Gigafactories incorporate energy-efficient systems and utilize renewable energy sources.
This outdoor clothing company is committed to environmental responsibility. They have implemented a Worn Wear program, encouraging customers to trade in used clothing for store credit and repair damaged garments, extending their life.
Unilever has made significant strides in reducing its environmental footprint. They set ambitious goals to eliminate waste, source sustainable raw materials, and reduce carbon emissions across their supply chain.
This global modular flooring company has made sustainability a core part of its business. Interface aims to have zero environmental footprint by 2020. They focus on reducing waste, using renewable materials, and recycling their products. Their “Mission Zero” initiative has not only reduced their environmental impact but also inspired other businesses to follow suit.
The Swedish furniture giant has committed to using 100% renewable and recycled materials in its products by 2030. They are also investing in sustainable forestry practices and energy-efficient manufacturing processes. IKEA’s sustainability efforts go beyond product design; they also extend to packaging and transportation.
Ford is driving sustainability in the automotive industry. They’ve made significant strides in reducing the environmental impact of their manufacturing operations. For instance, their Rouge Complex in Michigan boasts one of the largest living roofs in the world, reducing stormwater runoff and providing natural insulation.
The fashion industry is known for its environmental impact, but H&M is changing that narrative. The company has introduced a circular fashion model, where they encourage customers to return old clothing for recycling. They also use sustainable materials like organic cotton and recycled polyester in their clothing lines.
The Evolving Landscape of Sustainable Manufacturing
As technology advances and awareness of environmental issues grows, sustainable manufacturing continues to evolve. Some emerging trends and innovations in this field include:
1. 3D Printing:
Additive manufacturing, or 3D printing, offers the potential to reduce material waste by building products layer by layer. It allows for more efficient use of resources and customization, leading to sustainable production.
2. Circular Economy:
The circular economy concept is gaining traction. It focuses on designing products that can be easily disassembled, repaired, and recycled. Companies are exploring ways to extend the life of products through repair services and recycling programs.
3. Blockchain for Transparency:
Blockchain technology is being used to provide transparency in supply chains. This ensures that sustainable practices are maintained throughout the entire production process, from raw materials to end products.
4. Renewable Energy Integration:
Manufacturers are increasingly turning to renewable energy sources such as solar and wind power to reduce their carbon footprint. This not only reduces emissions but also lowers long-term energy costs.
5. Smart Materials:
Advancements in materials science are leading to the development of sustainable materials that are stronger, lighter, and more eco-friendly. These materials can replace traditional ones with a higher environmental impact.
Conclusion
In a world where environmental sustainability is becoming a top priority, sustainable manufacturing is no longer an option; it’s a strategic imperative. Businesses that embrace sustainable practices, adopt smart manufacturing technologies, and align with the principles of Industry 4.0 are not only reducing their environmental footprint but also reaping financial benefits and enhancing their reputation.
As you embark on your sustainable manufacturing journey, remember that it’s not just about compliance with regulations; it’s about future-proofing your business. Sustainability is a path to resilience, innovation, and enduring success in an ever-changing global landscape.
By setting clear goals, adopting the latest technologies, and collaborating with like-minded partners, your business can not only thrive but also contribute to a greener and more sustainable future for all.