Identifying and Eliminating the 8 Types of Wastes From Your Organization
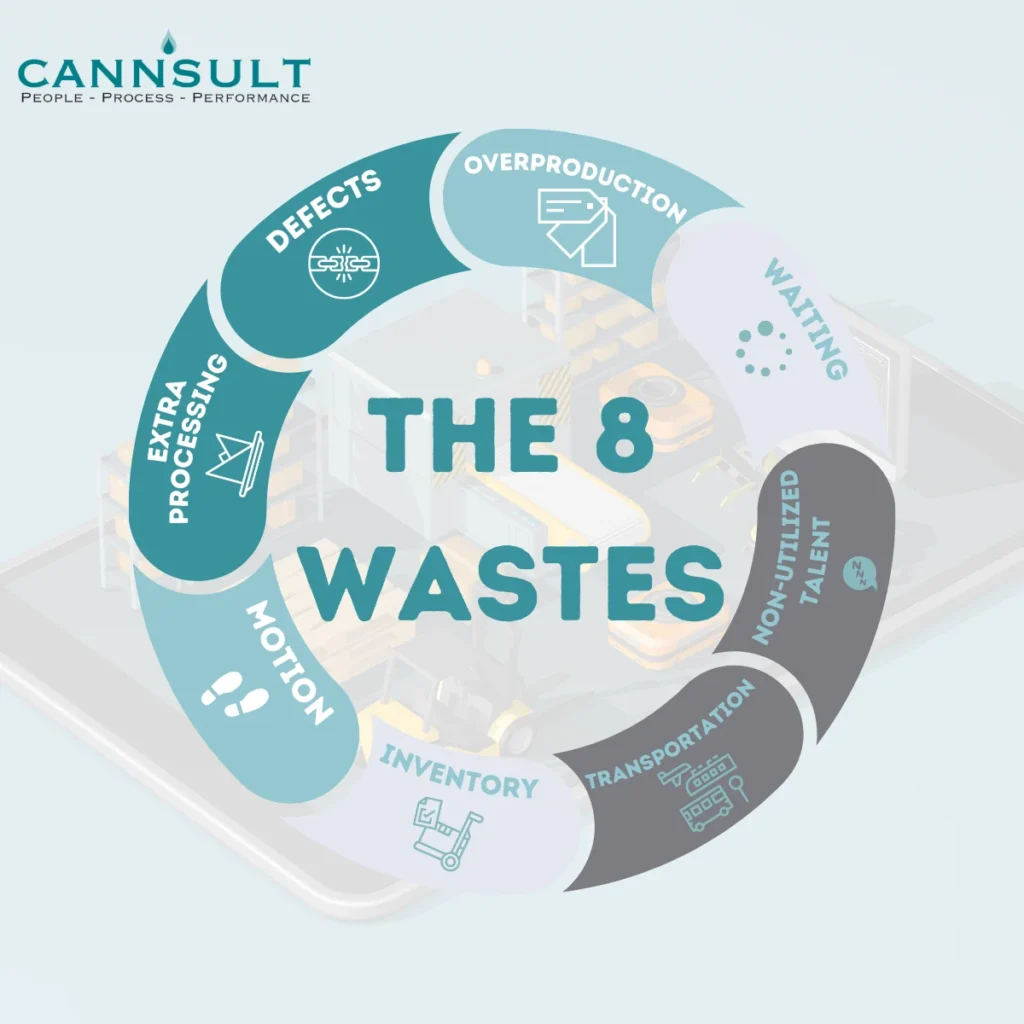
What is Waste?
When we think of the term, waste, it’s easy to picture things like garbage or wasted food that sat in the refrigerator for too long. Of course, these are accurate descriptions of waste. But when it comes to process improvement, we must be much more skillful in recognizing waste in our organizations. To understand waste, it helps to understand another Lean concept, which is Value. If we consider any step or task that takes place in any process, it can be classified as Value-Adding or Non-Value-Adding. In order for a step or task to be considered Value-Adding, it must meet all 3 of the following criteria:
The step or task must change the unit (or thing) going through the process. For example, if the “unit” going through the process is a Request for a Loan, we would evaluate the step in question to determine whether that Request has been changed. So, if the step is to wait for the system to upload the request, there has been no change. If the step is to review the Request, the Request has not changed. If, however, the Request has been assigned a unique number, it has been changed.
The step or task must be done right the first time. This means that any time we are performing steps that create an error, find an error, or fix an error, it is disqualified from being considered a Value Added step. Here’s where we learn that the need to perform a task does not equal “Value Adding”.
The customer must care. Some Lean practitioners will say “The customer must be willing to pay for it”. This doesn’t mean that we will actually charge the customer for this step. It is simply a way to align the step with what is important to the customer. So, if the step is to prepare a report for an internal status meeting, this is not likely something that the customer would care about.
Any step that meets all of the above criteria can be considered a Value-Adding step. And any step that fails any one of the above criteria is considered Non-Value Added. And this is the definition of “Waste”; steps that do not add value.
What are the 8 Wastes of Lean?
Any steps that are not Value Added are considered waste. Some are obvious and others are very counterintuitive. Some seem like they are valuable steps in the process and others are extremely frustrating – all of those frustrations, interruptions, and annoyances that get in the way of us doing our best work. Most of us understand waste to be physical waste or garbage…like scraps of wood on the floor of a wood shop or food that’s gone bad in the fridge. In any organization, identifying and eliminating process waste is a cornerstone of Lean. In a process improvement project, identifying the 8 wastes in our own processes is one of the main techniques to drive massive leaps in efficiency. Once the waste is eliminated – the results can be shocking!
Make no mistake, there will always be some amount of waste in every process, and the skill is learning first how to see it…and then to minimize or eliminate it! The trick is that you can only eliminate it if you can see it. And process waste is clever. It hides in every nook and cranny of the process, camouflaging itself as critical or necessary. And therein lies the problem!
We could either examine our process for all the thousands of specific types of waste, OR we can learn the 8 categories of waste that all waste falls into. This makes it much easier to recognize and then get rid of it. So, here we are. The 8 Wastes of Lean are:
Defects
Overproduction
Waiting
Non-Utilized Talent
Transportation
Inventory
Motion
Extra-Processing
1. Defects
Defects, errors, mistakes…anything that is less than perfect is considered a defect. In many processes, there are multiple opportunities for errors. And the easier it is to make an error, the more costly the process and the fewer happy customers. Examples of defects could be rejects, mistakes, errors, repairs, and rework. Defects always require some amount of additional attention, as they normally come at a tremendous cost to companies and organizations. A simple guideline that is easy to remember is that it costs $10 to make a mistake, $100 to find it, and $1000 to fix it!
2. Overproduction
This is simply creating something before it’s needed or creating more than will be used. This is a broad category that applies to many different scenarios. In a manufacturing environment, it might be creating more parts than are necessary. In the service industry, it might be preparing food for 100 people when only 50 customers were booked. For most people, we can relate to preparing reports, presentations, and documents that never see the light of day. Overproduction is also connected to the other 7 wastes, as it tends to amplify them in all scenarios. In the worst cases, overproduction can lead to lower quality and lower productivity and can make it significantly more difficult to identify defects.
3. Waiting
This waste is simple to understand and can be found throughout every process. When we create detailed process maps, one of the most shocking activities is to identify any spot in the process map where the unit going through the process waits. For example, we might say that the first 3 steps are: 1. Submit Request, 2. Enter the Request in the System, and 3. Approve Request. If we were to add the “waits”, it might look like this: 1. Submit Request, 2. WAIT in the queue, 3. Receive Request, 4. WAIT in the queue, 5. Review Request, 6. Submit to Approver, 7. WAIT in Approver’s queue, 8. Approve Request. When we add up the proportion of steps that are waiting and we total up the amount of time that any given “unit” sits and waits, the numbers can be shocking!
4. Non-Utilized Talent
Non-utilized talent can also be classified as non-use, misuse, or underutilization of human resources. A company or organization can get the most out of its people where the people can apply their strengths most often. The strongest organizations we’ve worked with strive to unlock the full potential of the people doing the work, and where everyone can contribute to varying degrees. This type of waste is much more difficult to recognize and can be even more challenging to fix. When we have people in positions where a significant amount of time is spent on non-value activities, they certainly do not have the opportunity for peak performance. In addition, when our infrastructure is not set up to tap into the innovative ideas and potential contributions of the people who work closely in the process, it is a huge waste of our most valuable resources.
5. Transportation
This refers to moving something through the process. Transportation adds no tangible value and is only a cost to the company or organization. Transportation can be physical (like moving a product on a truck or airplane), but can also be digital (sending information via email). In any process, we must identify the “unit” going through the process… an order, a request, ingredients, parts, etc. If we were to follow one unit going through a process, we could track how many times that unit was moved from one place to another. Each of these moves adds costs, and time and opens up opportunities for defects. If we run a coffee shop, we might use the example of receiving a box of fresh coffee beans. How many times might that box of coffee beans move from the time it arrives to the time that it is consumed?
6. Motion
Where transportation is the movement of the materials or items going through the process, motion refers to the unnecessary movement of the workers in the process. For example, walking an extra ten steps from one station to the next, when they could be moved closer together. This is a good example of a waste that at a glance may seem harmless, but spread out over months and years come to miles of wasted motion. In a doctor’s office, the patient might be the “unit” going through the process. And the patient might get moved from the check-in desk to the waiting room to the nurse’s room to the exam room and then to the check-out desk. How would minimizing this transportation help the patient experience?
7. Inventory
Inventory waste is the unnecessary surplus of inventory. Sometimes this waste is also referred to as a working queue such as work waiting to be done or an inbox of unread emails. Excessive inventory is one of the most costly wastes as inventory requires storage, management, auditing, and many inventory items can become outdated or obsolete. The balance that we strive to achieve is having just the right amount of inventory to ensure that work is not delayed waiting for supplies while minimizing the unnecessary costs and risks of too much inventory.
8. Extra-Processing
This waste describes when complex methods are used when a simpler, less-complex method would do. This is another waste that can amplify any of the other wastes because it creates more time and more steps to deal with already-complex issues. Examples could be over-polishing parts, sorting files that don’t need sorting, excessive cleaning, or excessive data collection.
Pro Tip! A simple way to remember the 8 Wastes is to use an acronym. The most common are DOWNTIME and TIM WOODS, each containing the initials of a type of waste. In the case of TIM WOODS, the second “O” is for “over-processing” instead of “extra-processing”, and the “S” stands for “skills-unused” instead of “non-utilized talent”.
One thing to know about waste is that it is fantastic at camouflage and blends really well into our processes.
Waste Calculation
When you track it and measure it, you’ll quickly see this seemingly harmless little bit of waste multiples over weeks, months, and years. It sucks the dollars out of your profit and the precious time and energy out of employees. Below is a real-life calculation from an organization that identified waste in the seemingly innocuous task of walking back and forth from the printer…
Sometimes, waste is SO embedded in our processes, that visualizing it on a process map is the best way to SEE it! It can be especially challenging if the person searching for the waste has been in that position and that environment for a very long time. Therefore, a crucial part of identifying waste is to first map out the process you are focusing on, giving the whole team an actual visual of the process flow.
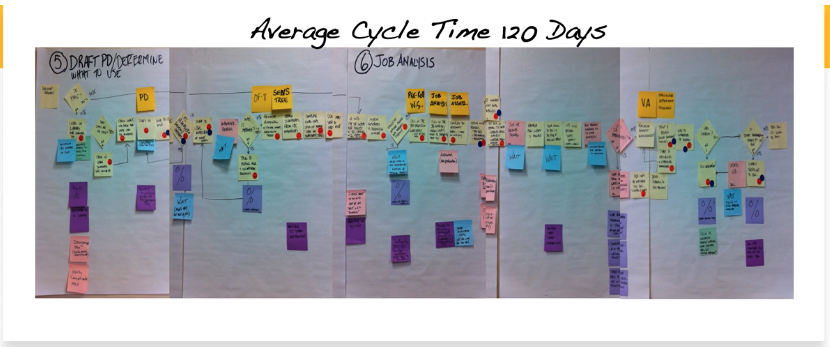
In Cannsult’s 8 waste course, we walk you through a real-life example from a government agency working to find waste in their job posting process. Our Lean Six Sigma Master Black Belts helped them put together a process map, where the team worked with them to identify waste on the physical map (spoiler alert! Every sticky dot, pink stickies, and purple stickies indicates waste!).